Although the cloths themselves seem simple, the production process requires a steady hand and the eyes of a true artisan. The entire process involves up to ten craftsmen!
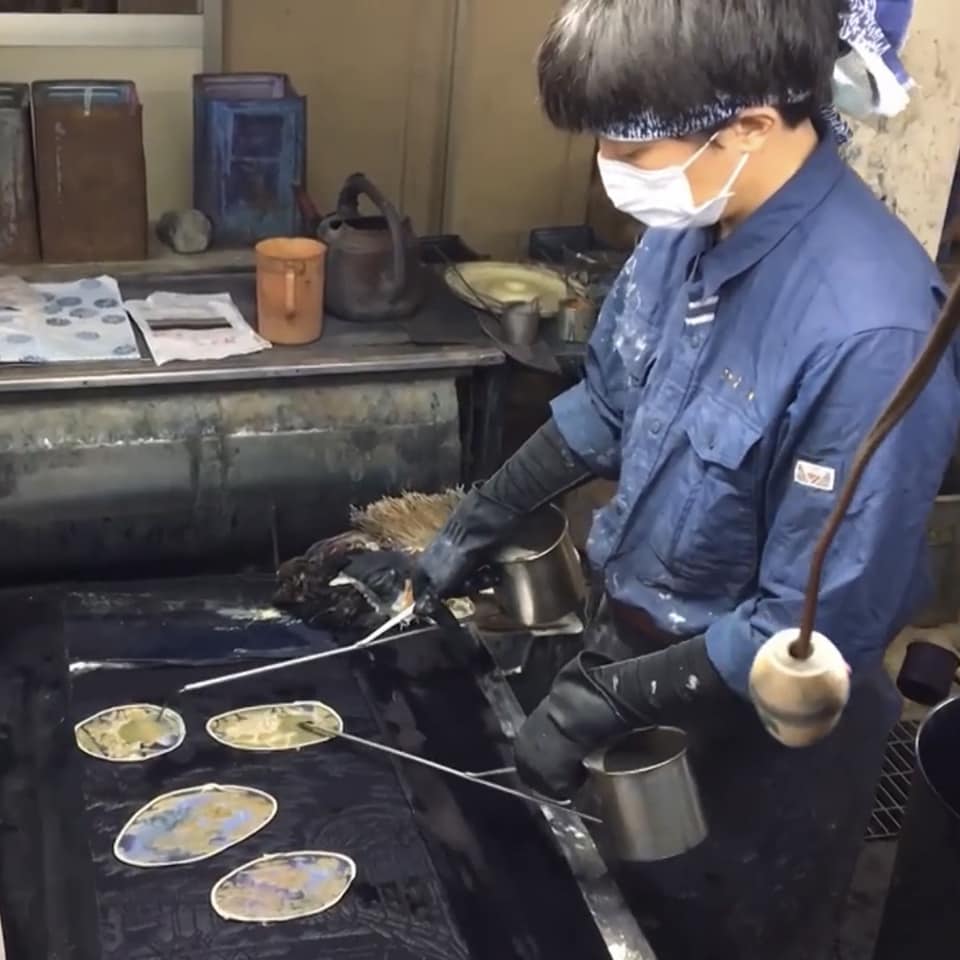
RIENZOME
Rienzome has been established in 1872 and beautifully crafts a variety of cotton textiles. From Tenugui, multi-purpose cotton towels that can be used as bandana, to wrap things or for decoration as wall tapestry; to Jinbei - Jinbei, a casual clothing for kids that can be used indoors or as pyjama. Noren curtains are dividers that hang at the entrance of a building or between rooms. And their scarves are popular year-round for their softness and traditional designs.
Chusen Dyeing
Rienzome uses the ‘Chusen’ dying method, which is a hand dying technique that results in an intense print visible equally on both sides of the cloth, whereas printed versions will have one good- and one bad side.
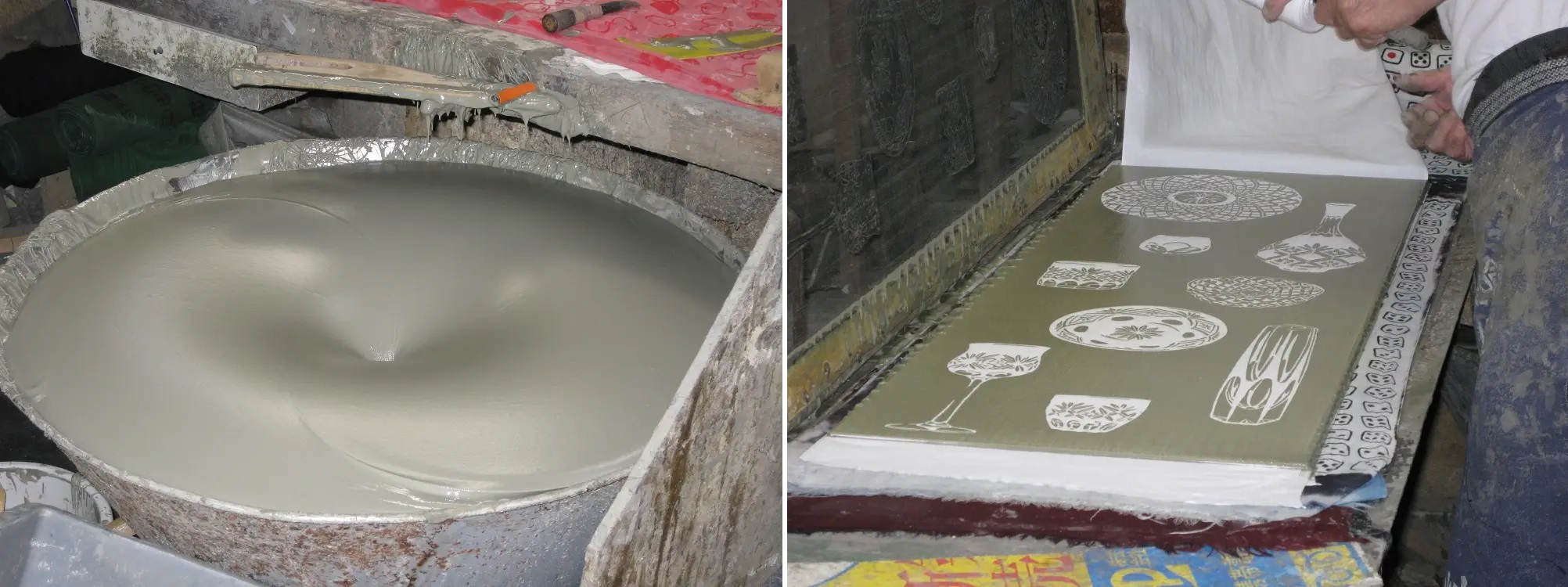
First of all, the fabric’s pattern will be drawn and carefully carved out on a special stencil paper. A bleach specialist is required to prepare the cotton cloths to get painted.
It requires a mixture of seaweed and starch that helps keep the parts of cloth that do not need to be colored, clean. Several layers of cloth are painted at the same time, which means the artisan needs to be very careful, as once he makes a mistake, the entire roll of cloth will be wasted. The starch-seaweed mixture is applied on each new layer and is also used to creates small dams around different areas where the paint with get captured in order to color patterns and decorations.

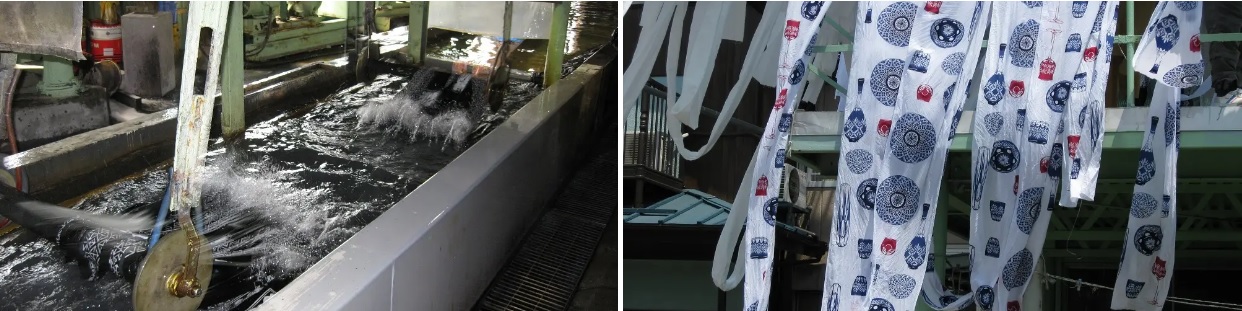
Then, heated dye is released on top of the cloth and should only cover the parts left uncovered with the starch mixture.
Craftsman often pour using a water can and with two hands at the same time! A vacuum below the cloth, operated with a foot pump, will pump all the paint down, allowing multiple layers to be dyed at once. The cloth then needs to be turned around so that the process can be repeated on the other side. Craftsman have to be extremely precise throughout the entire crafting process in order for the final result to be successful.
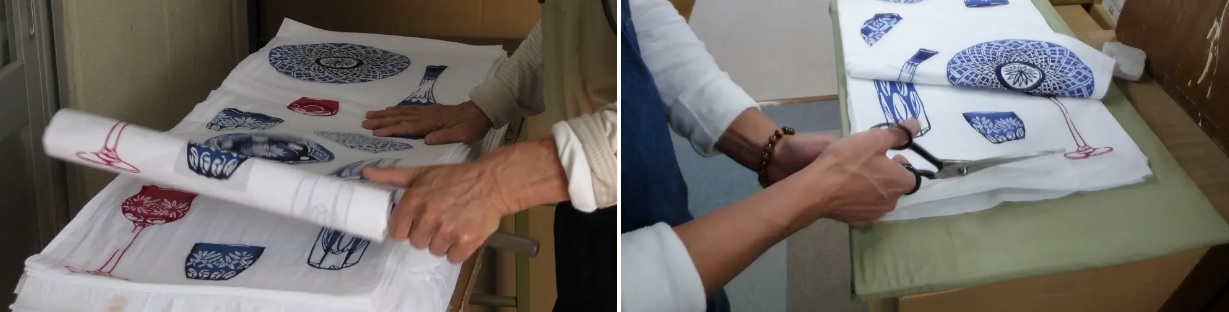
Finally, the painted cloths are washed in water to remove all the starch, left to sundry and rolled with a machine to remove all the wrinkles. The cloth is then cut in smaller pieces depending on its intended use as tenugui towel or clothing.