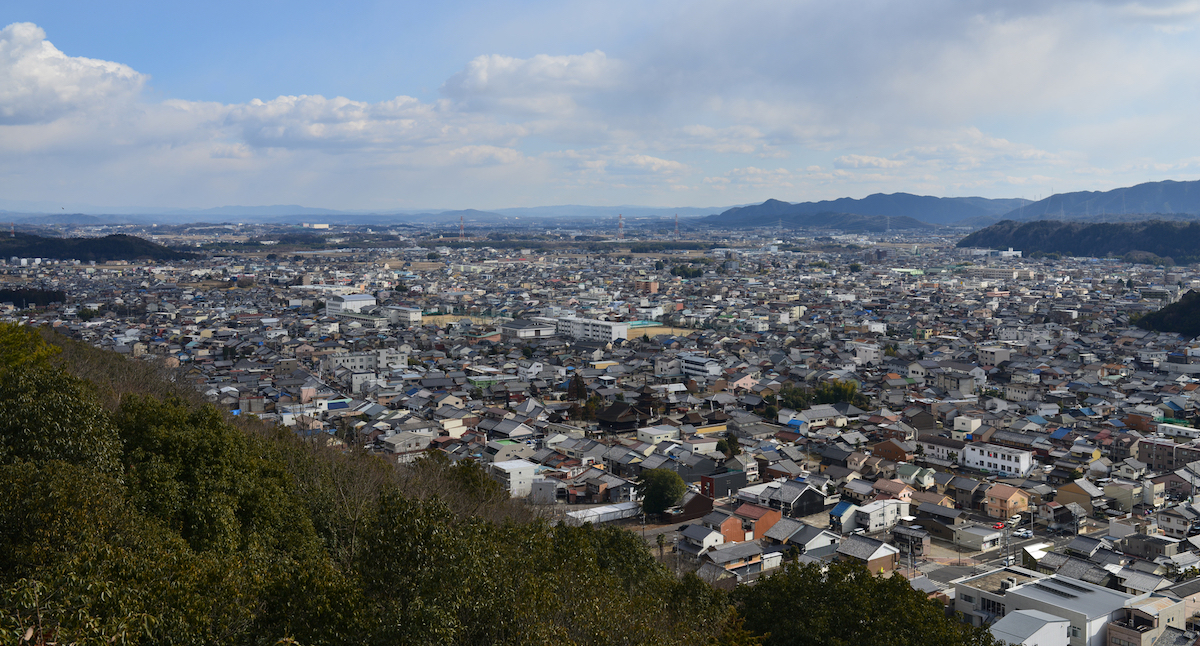
800 years of history
HASEGAWA is based in Seki City, Gifu Prefecture; a "cutlery town" blessed with lush mountains, pure rivers, and a beautiful natural environment. Blade making began in Seki City more than 800 years ago in the Kamakura period. It is said that a sword ancestor named Motoshige visited this area, discovered high-quality incendiary clay, which is the raw material for swords, and started swordsmithing. Seki's swors were favored by many warlords for their excellent practicality and artistry.
After the "The Sword Abolishment Edict" in the Meiji period (1786), production fully swifted to kitchen knives and other household blades.
Seki City has become a recognized world-class brand for high-quality and design-rich blades as one of the top 3 blade production areas in the world. The city still hosts big events to celebrate their cutlery culture, including the "Cutlery Festival", the "Knife Memorial Festival" and the "Ancient Japan Sword Forging Ceremony".
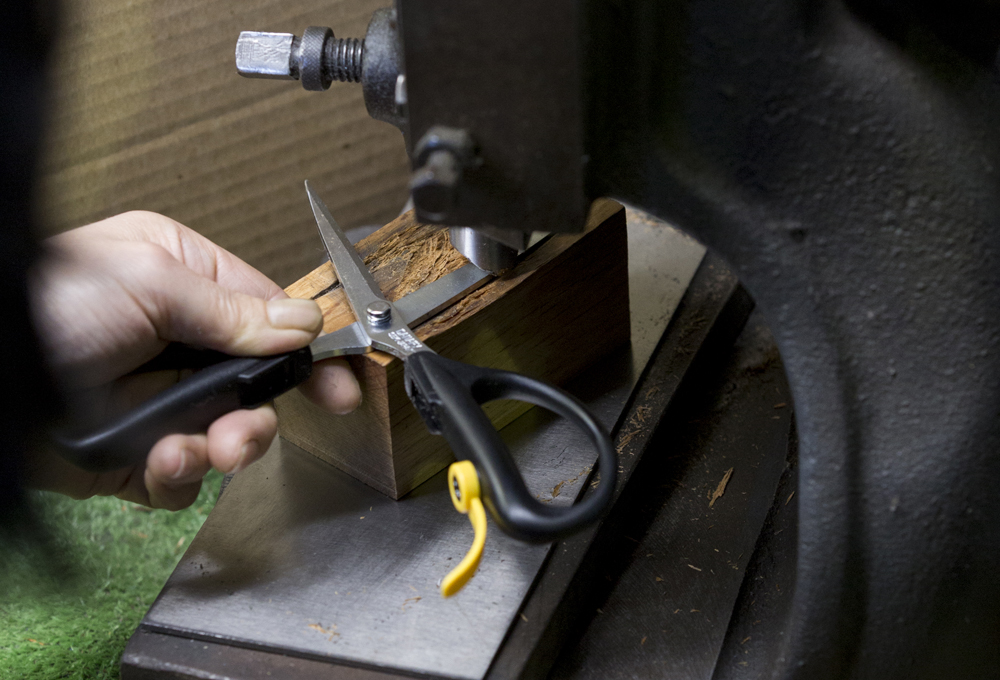
HASEGAWA has a history of over 80 years and attributes their success to the best technology, craftsmanship and trust of their users. To create trust, they focus on listening to their customers and answer to customer needs. Examples are safe knives and nail clippers that could be used without using force or the risk of cutting yourself - perfect for elderly and kids; as well as emergency cutters to cut seat belts and break windows.
They create over 130 different cutters and blades ranging from simple, but excellent standard scissors, handy standing desk scissors, to specific cutters for cardboard, grass or paper. They place an importance on "nature and people" and have won several awards, including for offering a great workplace for women, business continuity and s SDGs declaration.
Although good technology is an important part of the HASEGAWA manufacturing style, many steps are still done by hand by skilled craftsman, to ensure perfection for every blade.
Production Process
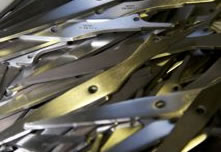
The "blade" that is the source of the blade is made from a plate-shaped steel material.
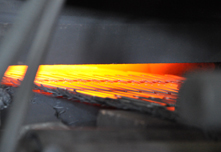
1000°C heat is applied to the blade. Heating and cooling are used to obtain hardness.
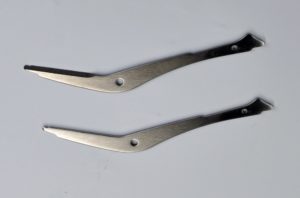
Sharpened with a whetstone and attach with 1/100mm increments.
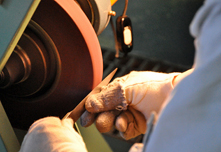
While beautifully processing the surface of the blade, the shape is adjusted.
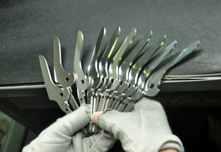
Manually check the blades for small scratches and rust one by one.
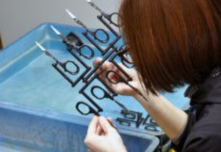
The melted resin is poured into the mold and the handle part of the scissors is molded.
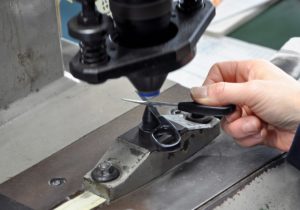
Two blades are carefully squeezed into one pair of scissors and different angles attached.
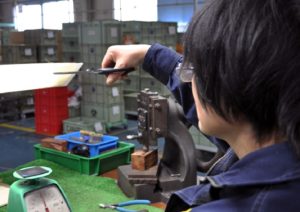
Final engagement is adjusted one-by-one and the items are packed to be sold.