Toyohashi brushes are famous for holding up ink very well,
so you can focus on writing, without having to dip several times.
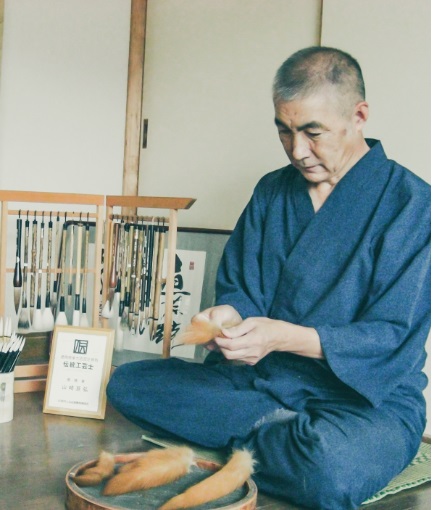
Mr. Yamazaki established Toyohashi in 1958, in Toyohashi city, Aichi prefecture. He is extremely committed to the preservation and development of the traditional Toyohashi brush and is steadily working to pass on the traditional craft. Other than his "Traditional Craftsman Certification" he has received several awards for his skill and contribution to the traditional craft.
Traditional brushmaking crafting has been passed down since the Edo period. Craftsmen like Yamazaki, execute all 36(!) processes to finish a perfect brush. Next to craftsmanship, knowledge and experience is also needed to recognize and properly select the right hair types for each brush function and how to work with them to create the best brush for each combination of hair types.
With demand for brushes diminishing over time due to changing cultures, a modernizing society and the shrinking of traditional markets, Toyohashi is especially motivated to keep their precious art alive and support the Toyohashi region.
Through workshops in schools, offering brush crafting workshops in their workshop and teaching people about the beauty and quality of a handmade traditional brushes, they hope to preserve and develop the brush culture, in- and outside of Japan. They work closely with other craftsmen, as traditional art styles like calligraphy, require not just a great brush, but great ink and washi paper to be practised.
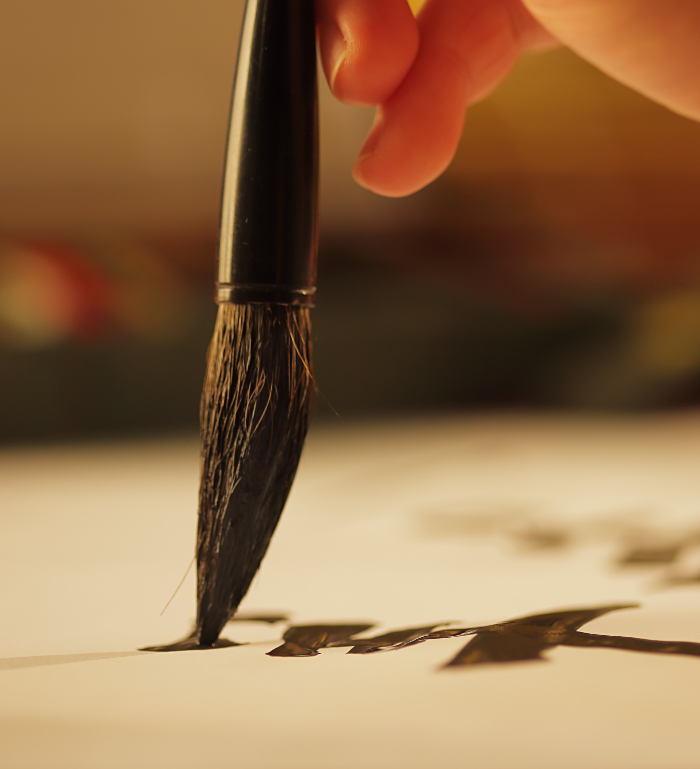
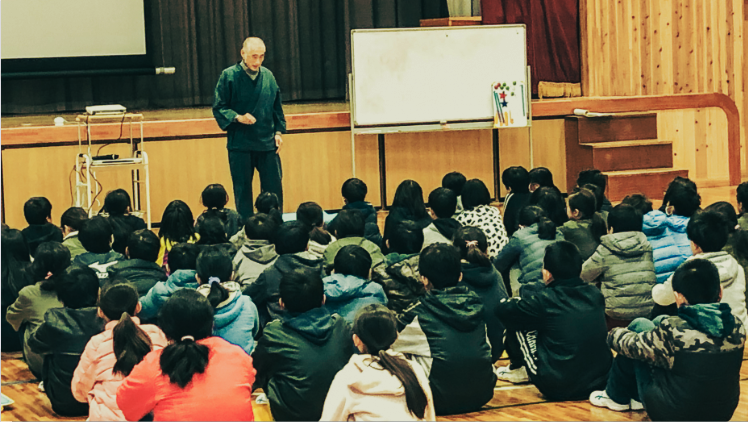
The Toyohashi brushes are made using a special technique called "kneading" that results in excellent retention, so that the brush hairs soak up and hold the ink.
Deeply understading the characteristics of various animal hairs and using and mixing hairs with different spikes, length, thickness, hardness and elasticity, hundreds of types of brushes are made for calligraphy, paintings, daily use, etc. Toyohashi brushes are well reviewed for their stability, durability and high quality.
During the Edo period, Toyohashi was a castle town of the "Yoshida clan". When the Yoshida clan was facing financial difficulties, low-class samurai started crafting brushes as a side job, which would be the beginning of the Toyohashi brush craft. Since Toyohashi is located in a mountainous area, it was easy to procure materials for making brushes, and because it was located on the important "Tokaido Road", used for trading and traveling, the brushes made in Toyohashi quickly spread throughout the country. In 1976, it was officially designated as a traditional craft.
Brush Hair Types
Raw hair still attached to the skin is sheared one by one with a knife, without using chemicals, so that the
hair is not damaged and stays strong, without losing elasticity and durability.
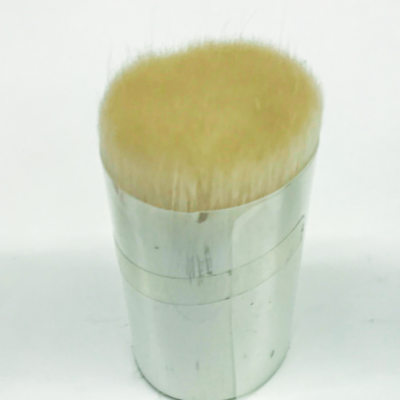
Goat
The tips are sharp, the ink retention is very good, and the hair is very soft. Used for woolen brushes.
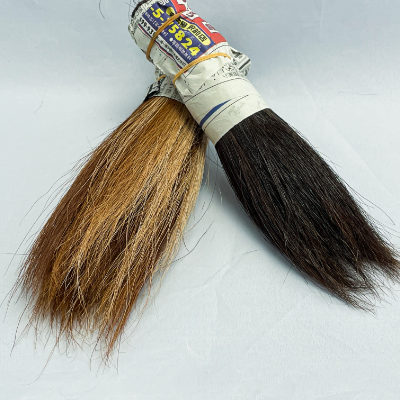
Horse
Has moderate elasticity, uses different hairs on each part such as tail or mane, and is used for thick- or oversized brushes.
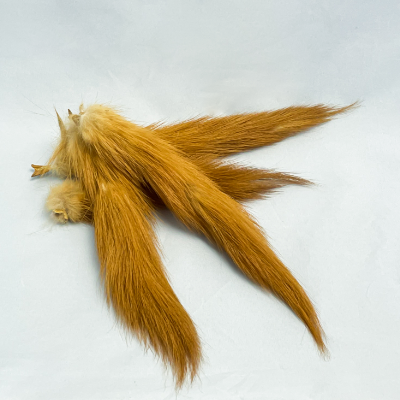
Weasel
With elastic and ink-bearing bristles, used for fine brushes. Weasel and Corinsky sable hair are currently difficult to obtain.
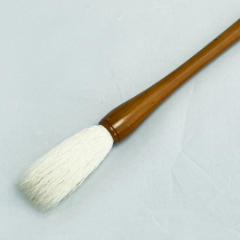
Fawn
The bristles are coarse and elastic, so they are used for the waist of thick brushes.
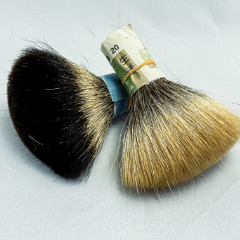
Tanuki
Very elastic and voluminous bristle at the tip, and is mainly used in combination with other raw hairs.
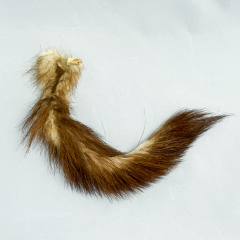
Squirrel
It is very soft and sticky, and feels good on the skin, so it is mainly used for makeup brushes.
Crafting the perfect brush
There are 36 manufacturing steps for Toyohashi brushes. The brushes are amde by hand through the craftsmanship inherited from the Edo period. It can be shown in 6 steps:
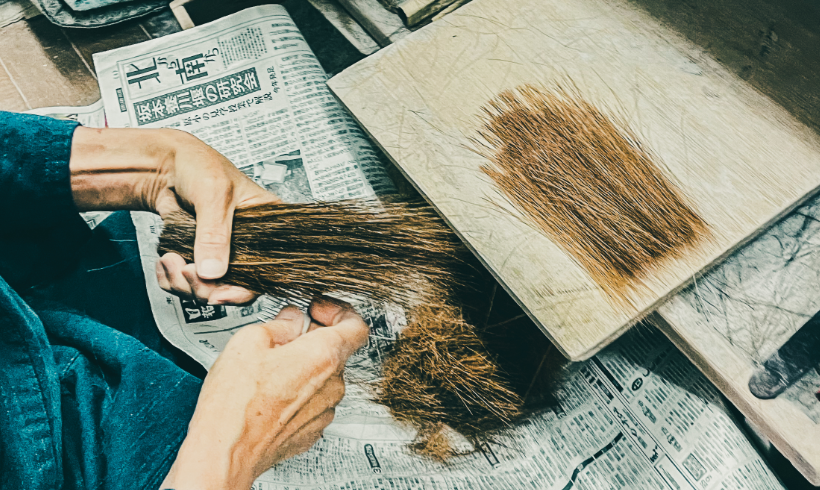
Sorting
Raw hair is sorted by eye, and handled by hand according to its purpose. Length, quality of hair tip, etc. are all taken into account.
Heat is applied to remove moisture and straighten the hairs.
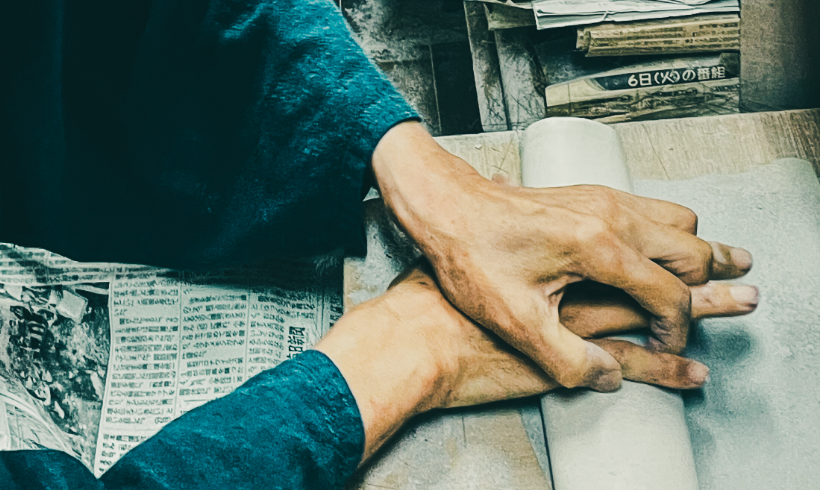
Hair firs
The raw hair selected in step 1 is sprinkled with ash made by baking rice husks, and in order to remove fat and improve the absorption of ink, wrap deer skin around the hair and rub it strongly with both hands. The tips of the hair are tied together, tied with hemp thread, boiled, and spread out into a flat shape with a gold comb.
Then, the tips are brought together and sorted and aligned.
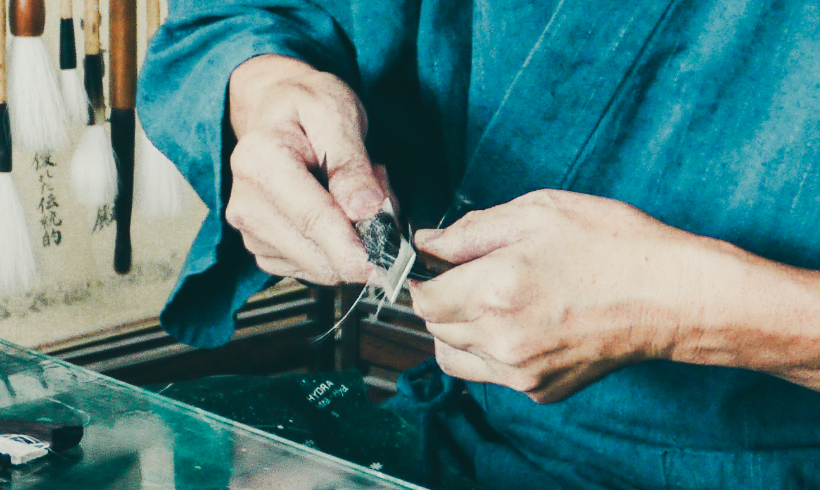
Combing
The hair aligned at the tips is carefully plowed with a gold comb so that the hairs are not entangled or bent, the hairs are straightened to align the tips.
Finally, the shape is adjusted using a hammer on the glass plate.

Kneading
Toyohashi's unique technique and the most characteristic process in Toyohashi brush making.
The hairs soaked in water are mixed, so that the hairs mix evenly. The ink retention improves so that the hairs easily blend with ink. After sorting, the core hairs were sorted and processed seperartely based on hair type, and can now be mixed together again through "rough mixing" and then "total mixing". Finally, plucking is used to clean out any inferior hairs.
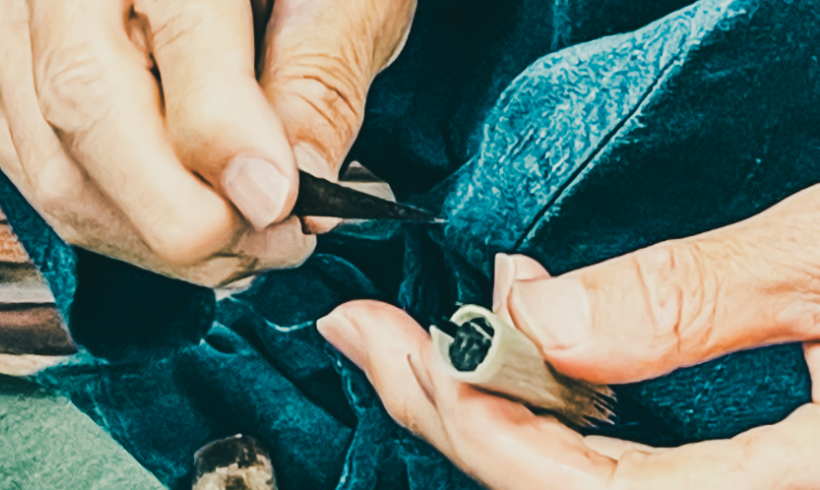
Centering and coring
Hairs for the core are inserted into the tops (mold) using "hansashi", to create the shape of the core. They are then dried in the sun.
The upper hair is wrapped onto it and neatly plowed up with a metal comb, stretched thinly, wrapped around the core and then dried
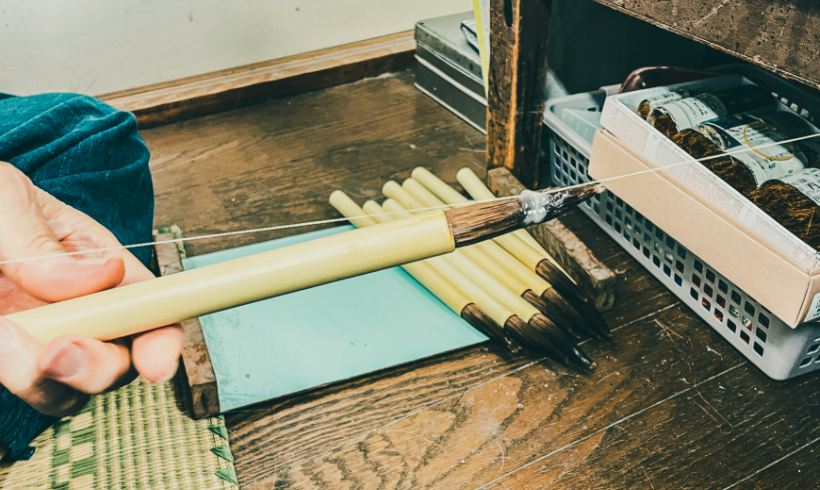
Finishing touches
The dried "ears" are tied with hemp thread, the tails are tightened, baked with a grilled iron and tied up, glued to the shaft, and the ears are inserted. After the entire panicle is soaked with glue, made from seaweed, the thread is wrapped around the root and the excess glue is removed while turning the shaft. The panicle is then shaped and dried.
Finally, in order to protect the tip, each scabbard is applied to the dried brush. To complete, the brush is engraved if needed.