KIRIMOTO's mission is to have people use “wood" and "lacquer” more in modern everyday life. The Kirimoto family has therefore been dedicated to wood and urushi lacquerware product development for more than 200 years in Wajima, Ishikawa prefecture. Since the 18th century, they have over time specialized in carving the core wooden fittings. The highly talented team of craftsmen now create wooden and lacquer vessels, furniture, and interior elements, exploring the possibilities of wood and "urushi" lacquer as a part of modern lifestyles.

Wajima Lacquer
Wajima Kirimoto is one of Japan's most prestigious brands for lacquer ware. The company was founded during the Edo period and is is now run by the 7th generation of the Kirimoto family. Kirimoto is located in Wajima city in the Ishikawa prefecture and therefore is a typical producer of "Wajima lacquer". The beauty of Kirimoto products comes from the combination of traditional lacquer techniques with contemporary designs. They are one of the most innovative producers of lacquer ware.
The famed durability of Wajima lacquer ware is the result of both the high quality of the lacquer refining process and the composition of the undercoatings unique to Wajima. A finely powdered mineral called "jinoko" is used for the undercoating. This undercoating is much more durable than the rice powder, which is most commonly used to fix the lacquer to the wooden core. The special undercoating and the up to 8 layers of lacquer made Wajima lacquer so durable. Wajima is also famous for its chinkin style colored and metallic decoration called makie.
KIRIMOTO
The sixth generation of the Kirimoto family, Shunbei, took over the family business immediately after graduating from high school.
During this time they focused especially on Japanese-style rooms and Western-style furniture in general. They over time established a woodworking shop that handles special wood fabrics and furniture.
Seventh generation Taiichi Kirimoto majored in product design in university, and after apprenticing as a wood core maker, he started producing wood modeling and design proposals, and has overseen the overall direction of lacquer production. Since 2015, the talented craftspeople of the company produce wooden and lacquer vessels, furniture, and interior elements, exploring the possibilities of wood and Urushi lacquer as a part of modern lifestyles.
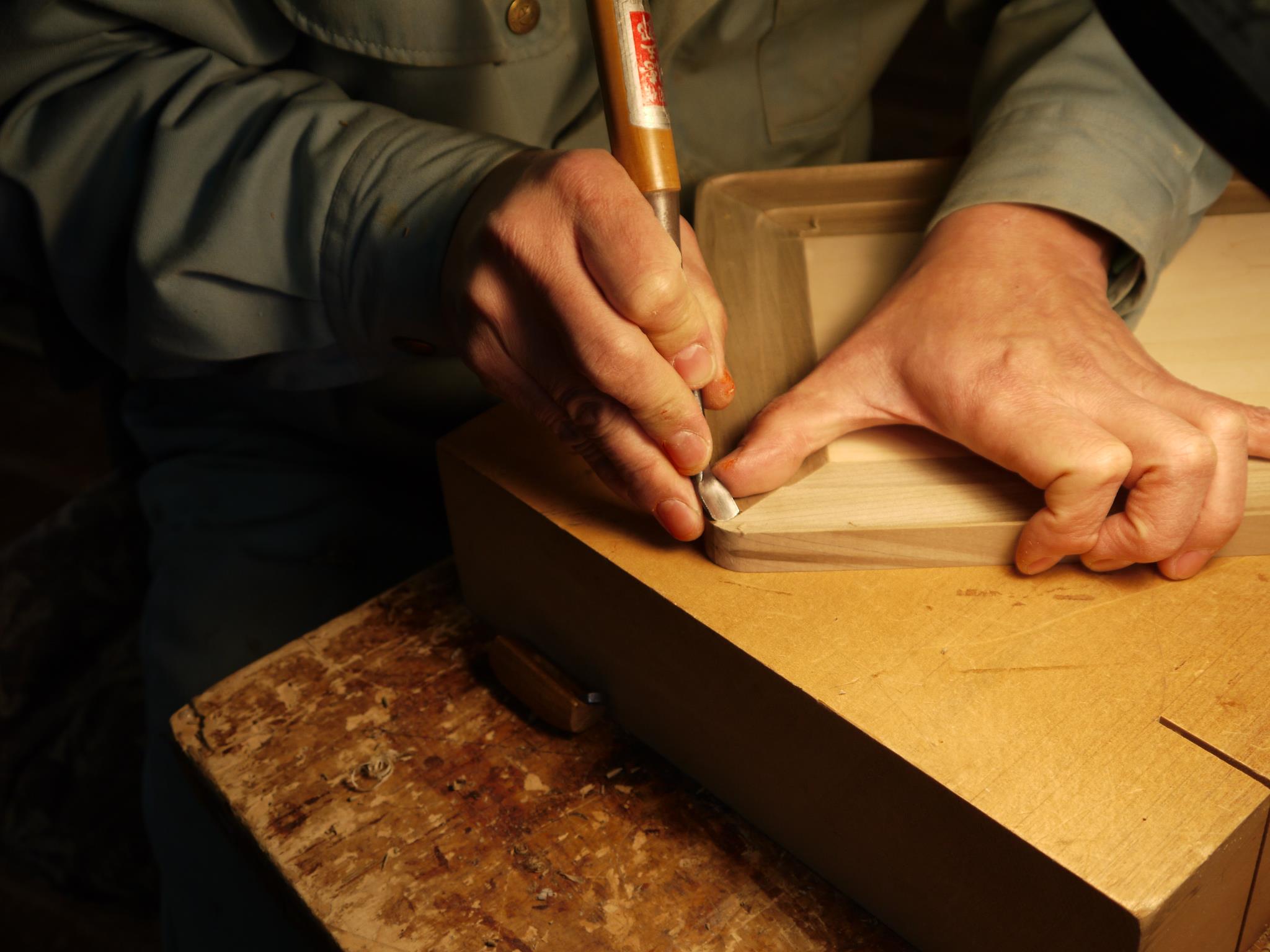
KIRIMOTO Lacquer Styles
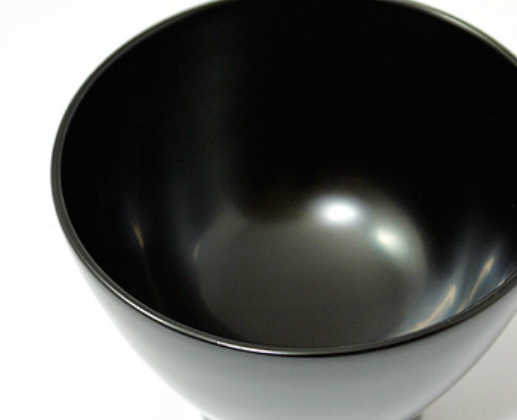
The Honkataji Technique
The standard techniques used to apply lacquer in Wajima. Lacquer cloth is applied to natural wood on the parts of the piece that are easily damaged, such as edges, base footings, the outside of boxes, or furniture tops. Then, diatomaceous earth collected from Mt. Komine in Wajima City that has been fired and made into a powder called "jinoko" is applied as a base coat. Then, it is polished, given a mid-coat, then a top coat. A cross section of a finished product would show nine layers in total. Even if the product is used for many years and the surface becomes damaged, it’s possible to be repaired.
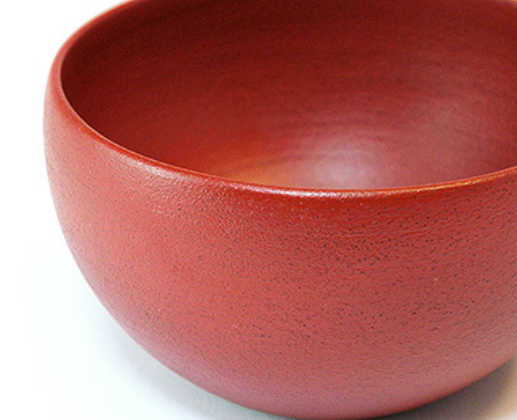
Wajima Kirimoto's Makiji Technique
Kirimoto took the makiji technique and successfully adapted it so that it creates a surface so tough that even a metal spoon used on the item will not damage it.
Lacquer cloth is applied to natural wood, and the jinoko that is used in the base coat is applied once again close to the surface. This technique is recognized by the Small and Medium Enterprise Agency as a “Manufacturing Program using Local Materials” and in 2007 it was chosen as part of the “Japanesque Modern Collection”.
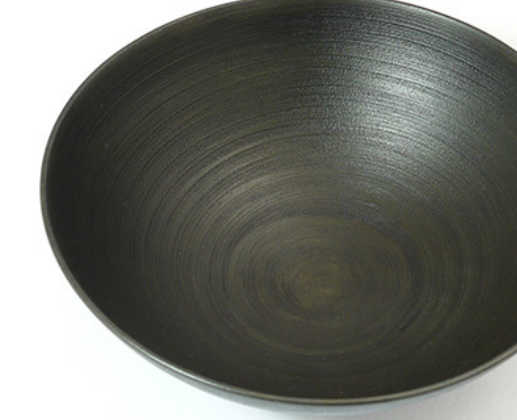
Wajima Kirimoto's Sensuji Technique
Sensuji finish is Kirimoto's original technique, which has the new expression of modern lacquerware. Lacquer cloth is applied to the natural wood on the parts of the piece that can be easily damaged. jinoko is applied too. Sensuji means "a thous and streaks" finish. Using a newly created special brush yields a bold "thousand streaks" pattern with plenty of jinoko, which makes the surface tough, and even engenders an antique expression. The combination of color of the deep lacquer with food and beverages is exquisite. It is hygienic and easy to care for and also safe with metal cutlery.
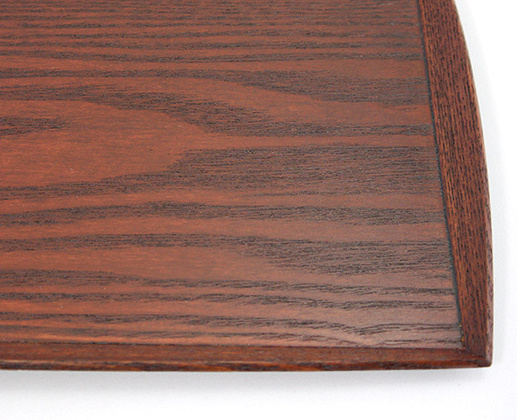
Fuki-urushi Technique
The most basic of lacquer application techniques. Lacquer is directly applied to wood that has been painstakingly cleared of all dust and fingerprints, then wiped off with a cloth before it dries. The lacquer is rubbed in to the wood as it is wiped off, and then the wood is dried. For bowls and spoons, this procedure is repeated 3-5 times. The gentle beauty of the wood grain is emphasized with this application technique.
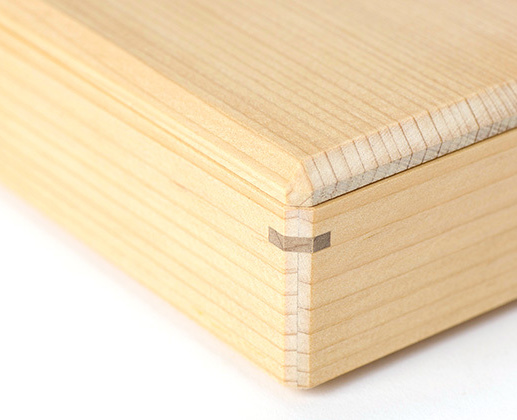
Wajima Kirimoto's Wood Products
At Kirimoto Wood Craft, the backbone of the company is its wood core manufacturing, which goes back 80 years. Lumber that has been aged for 10-20 years in order to make wood cores for lacquerware is also used to make wooden products for household use; Trays, plates, kitchen tools, small pieces of furniture, and more. Wajima’s native wood, "asunaro", is light yellow. Magnolia wood brought in mainly from Hokkaido and the Tohoku region is a gray-green color. They’re subtle shades, but they’re highly workable, and very water resistant. This wood is ideal for making items fit for everyday living.
The KIRIMOTO Team
All current craftsmen are born in Wajima and highly committed to share their culture with the world through exceptional craftsmanship.
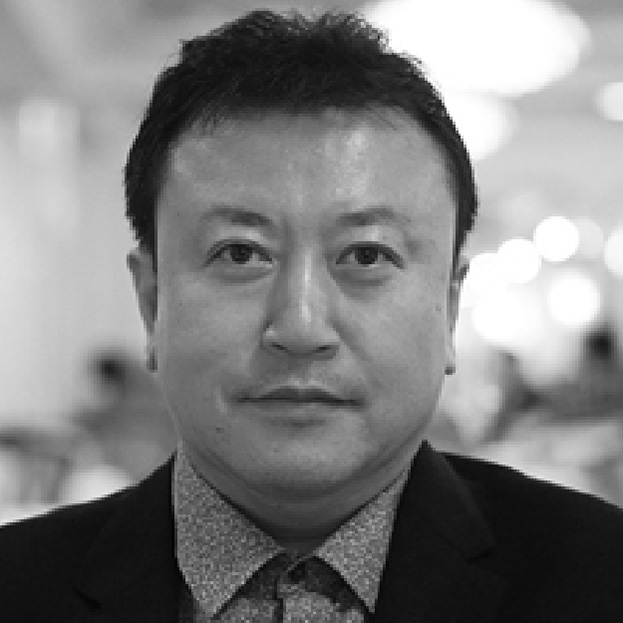
Mr. Kirimoto (7th generation)
"We will continue to making wood and lacquer a commonplace use in daily life.
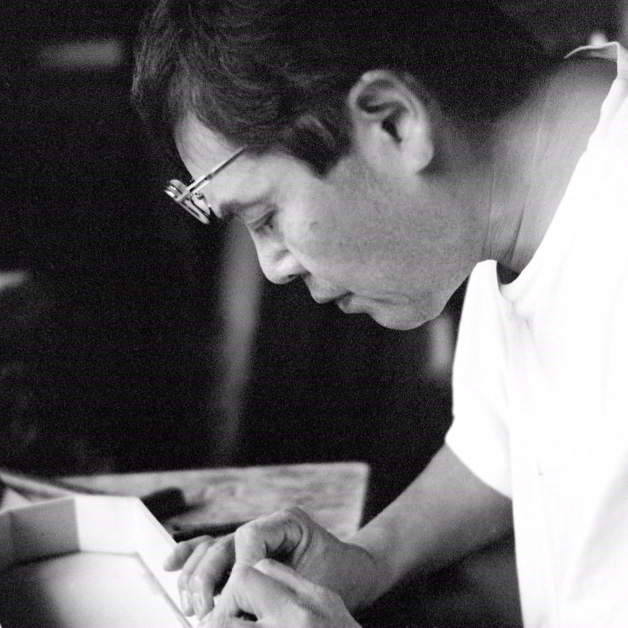
Mr. Sumi (cousin)
A veteran woodcutter with a reputation for advanced technology and careful work.
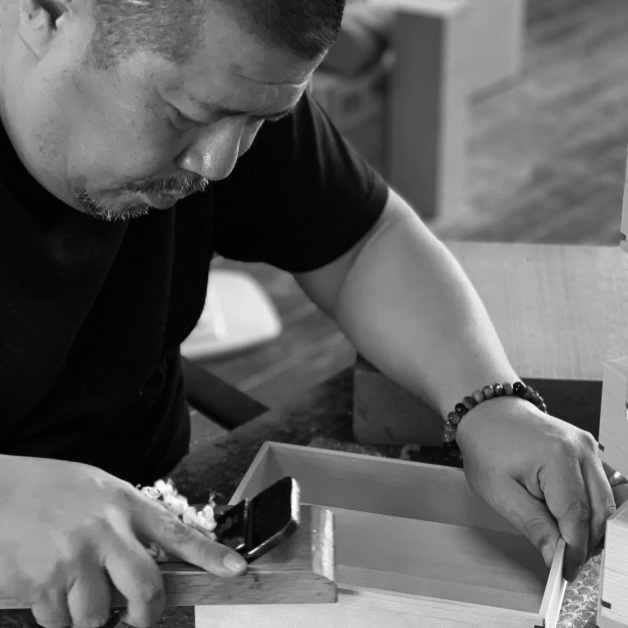
Mr. Kirimoto (cousin)
Wood processing and wiping lacquer. Favorite work: delicate processing with a small knife
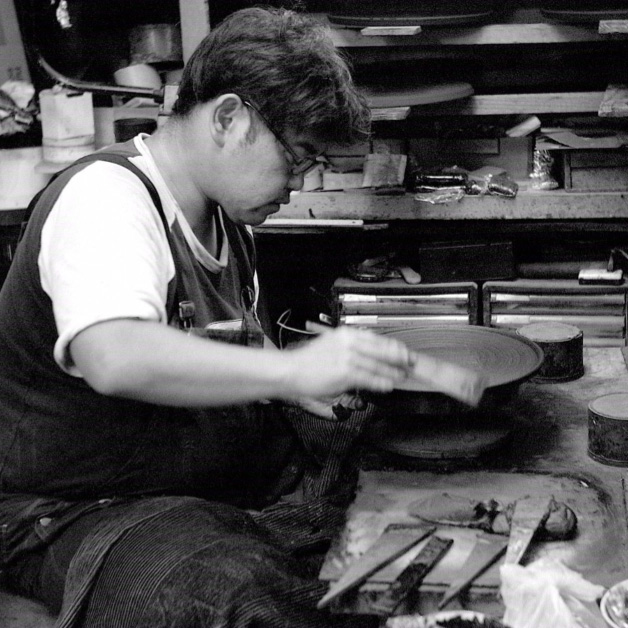
Mr. Koji
Lacquering. Started his career as a painter. Now in charge of the Sensuji and Makiji series and washi paper upholstery.
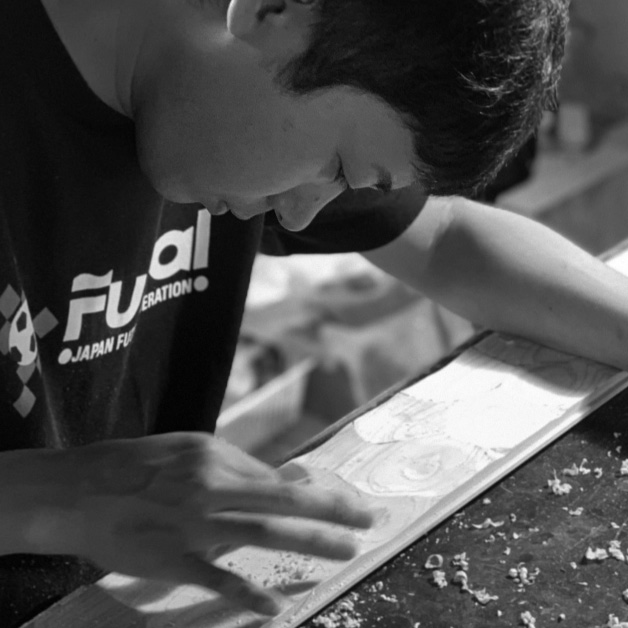
Mr. Kubota
He is in charge of design, wood processing, lacquering and sales. Specializes in cutting and cutting wood with small knives.
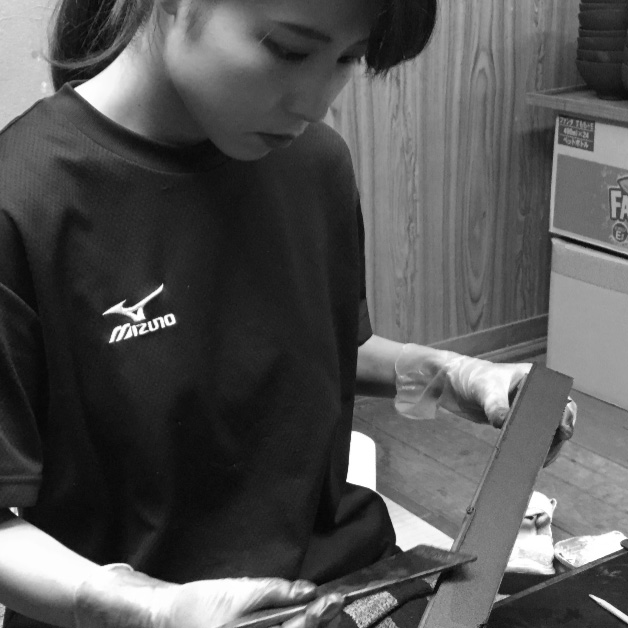
Ms. Imase (retired)
Lacquering. Kirimoto's first female craftsman. In charge of the overall groundwork of the main solid ground, using spatulas to curve.